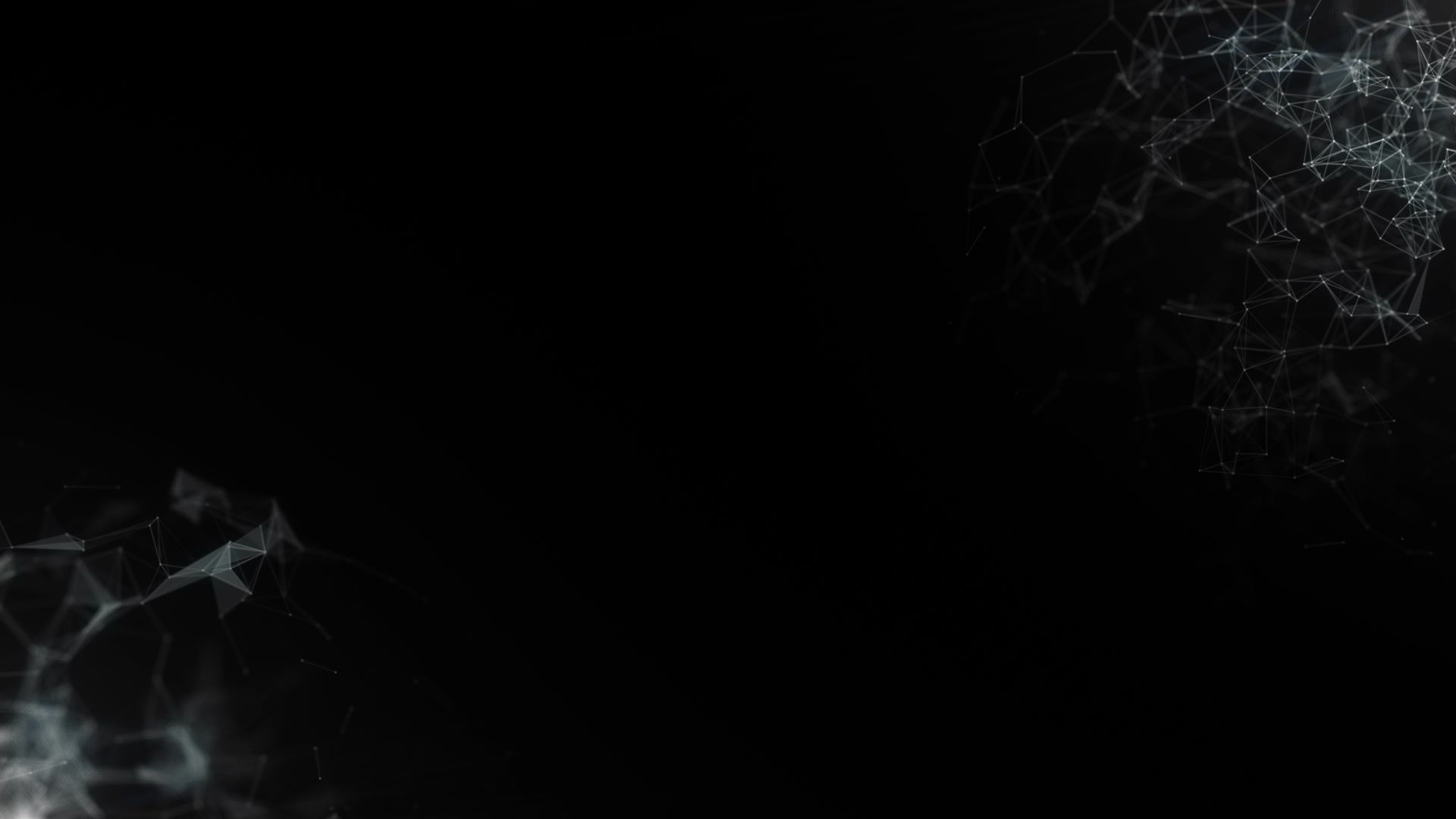
TIMELINE




Design Iteration 1
Design Iteration 2
Final Design
.png)
OVERVIEW
Redefining the Biopharmaceutical Industry
The biopharmaceutical industry was valued at over $200 billion in 2018, and is projected to reach almost $400 billion by 2024. Within this increasingly popular market, drug development remains one of the most important sectors. All biopharmaceuticals are required by law to meet certain properties to ensure safety and efficacy, and these properties must be monitored at all times. However, most current monitoring technologies actually tend to disturb the drugs, causing them to clump up and lose value. When this happens, production must be put on hold to replace expensive components, costing companies tens of thousands of dollars and valuable time. Our project aims to improve on the design and functionality of current monitoring technologies by removing the need for batch processing, ensuring zero disturbance to the process stream, and reducing the time and cost of cleaning by making contact materials cheap and disposable.
CUSTOMER NEEDS
Inline Process Stream
Device has no need to draw samples, and runs constantly
Improved Process Liquid Interface
Interface between the process liquid and the device is transparent, sterile, and disposable
Real-Time Results
Results are recorded and outputted to a computer for monitoring
FDA Approved
Contact materials used are FDA approved
MALS Performance
Device can perform Multi-Angle Light Scattering (MALS) measurements to obtain the molecular weight of a sample
Smooth Process Stream
Couplings between the disposable sleeve and the process stream are smooth and cause no perturbations
DATA ANALYSIS
.jpg)
How It
Works
Light scattering is the phenomenon that describes how molecules in a solution interact with light, causing it to scatter in different directions. Our light source consists of a linearly polarized laser, which is aligned such that it passes through the clear, disposable insert containing our solution. Light is then scattered in all directions, where it is picked up by fiber optic cables aligned at very precise angles. The intensity received by each of these angles is then processed by a computer. The Zimm analysis of static light scattering is used to determine the molecular weight. Everything must be extremely stable and precise, because even a misalignment of a couple microns can greatly affect accuracy.
Fluid Simulation
A flow simulation was created to observe the effect of any tubing diameter change. The video above shows that even with our maximum diameter difference from off-the-shelf parts, there is very little disturbance to the bulk fluid. The pictures below illustrate the difference in turbulence between our system, and that of a typical flow cell used in other devices at the same flow rate.
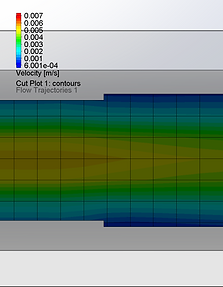
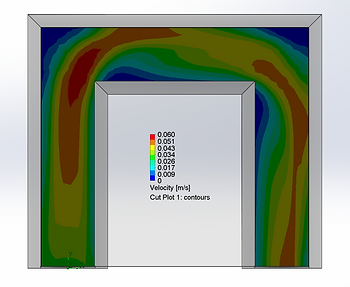
Noise Analysis

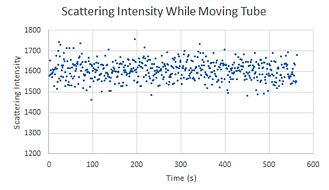
Noise analysis of stray light in AIMS system. On the left is a 20 minute time measurement of background light within the system upon boot up. This shows the importance of reaching laser stabilization before making a measurement, which normally takes 10-15 minutes. Data collection over several minutes under noisy conditions (i.e. vibrations) is shown in the photo on the right.
Light Modeling
A ray tracing program was used to model the effect of our tubing on the laser beam. The image on the right shows the refraction through BSG. Accounting for both refractive and reflective effects, the exit beam is reduced to about 50% the initial intensity. Experimentally, we see about 40%. This correction is included in the code when calculating molecular weight.

Code
Shown below is the visualization of light scattering. The fiber optic cables redirect the scattered light to an array of pixels on a CCD camera (shown on the x-axis). The peak information is recorded for both the baseline (left) and the sample itself (right). It is the difference between these two values that gives the molecular weight. This was all done using LabVIEW, and other third-party analysis softwares like Excel and Origin.


FINAL PRODUCT
Our final product is designed in such a way as to meet all of the customer needs and wants. The smooth connections between the process stream and the disposable interface result in no perturbations, and don't require samples to be drawn from the stream. Additionally, the laser and fiber optic cables are precisely aligned for maximum accuracy of real-time MALS measurements, used to determine the molecular weight distribution. Finally, the tubing for the liquid to flow through was carefully selected to ensure maximum transparency, sterility, and ease of disposal, while also conforming to FDA standards for contact materials. All of this was accomplished using $755 of our $1500 budget.
*Hover over for more details
3 cups
Blueberries
3 cups
Flour
Housing and Ceiling- encloses the CCD, fiber optic cables, laser and drill chucks to minimize stray light. Also provides stability and alignment for tubing
1½ cups
Butter
Drill Chuck- provides stability and alignment by clamping and not allowing tube to move
Glass Tube- provides much better scattering information than the plastic tubing used before
Our CAD Model
*Hover over for more details
3 cups
Blueberries
3 cups
Flour
Polarizer - Polarizes the laser beam perpendicular to the scattering plane
Flow Cell - Holds fiber optics in place and is situated around tube to collect best scattering data
Laser - Class IIIb laser beam sent through the tubing
Fiber optics - Collects scattered light and brings information to CCD
CCD - Collects data from fiber optics and serves as stepping stone to computer to portray data
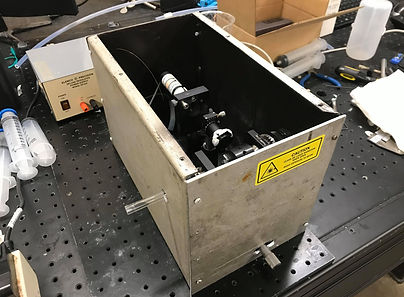

Working Prototype
THE TEAM
​
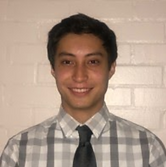
Zack Hartfield is a Senior at Tulane studying Engineering Physics with a certificate in Mechanical Engineering. Zack acts as the Project Lead/Software Developer
heads the coding & calculations, and assigns roles and tasks each week

Alex Burgers is a Senior at Tulane studying Engineering Physics with a certificate in Mechanical Engineering. Alex acts as the Design Coordinator, works on Assembly/Testing, and ensures that the design and tests match customer needs and specifications

Everest Shapiro is a Senior at Tulane studying Engineering Physics with a certificate in Mechanical Engineering. Everest acts as the Scribe, works on Assembly/Testing, heads Makerspace-related tasks, and takes notes
at meetings
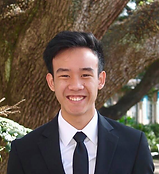.jpg)
Khoa-Andrew Nguyen is a Senior at Tulane studying Engineering Physics with a certificate in Mechanical Engineering. Khoa acts as the Budget Manager/Outreach coordinator and manages costs and purchases, writes weekly memos and emails, and maintains the website
Zack Hartfield
Team Lead - Software Developer
Alex Burgers
Design Coordinator - Assembly/Testing
Everest Shapiro
Scribe - Assembly/Testing
Khoa-Andrew Nguyen
Budget Manager - Outreach